The EV Battery Afterlife: Implications on the Climate
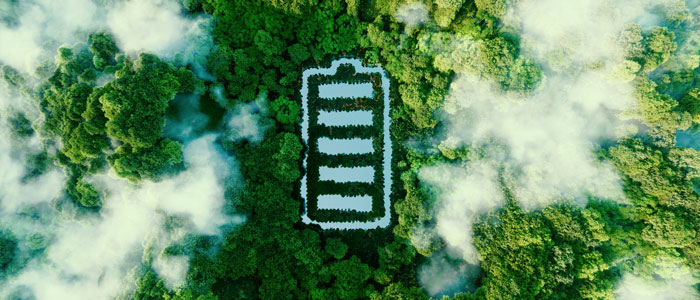
How is the EV industry gaining momentum as a medium to realize the net zero emission target worldwide?
The fight against climate change is more stringent today than ever. With the transportation sector contributing to >16% of the overall global carbon footprint, electric vehicles are proving to be a viable and promising alternative to enable net zero emission targets.
The past 5 years have seen a tremendous spike in EV sales across India and the world alike. Globally, the year 2021-22 witnessed an annual sale of 6.8 million vehicles, while India witnessed an overall sales volume of 0.3 million across vehicle platforms.
The EV sale in India rose by 168% from 2021 and is poised to further witness a CAGR of >40% over 2023-2030. While EVs are being popularly touted as the potent means to reduce carbon emissions, are we cognizant of the silent impact of EV batteries on the overall ecosystem?
By the year 2030, >40 million EVs are expected to be sold in India. Considering the average age of an EV battery being <5 years, we are staring at a possibility of >9 million batteries hitting the landfill by 2030. Taking this scenario into account, a question we must answer now is whether we are prepared to tackle the impending challenges. Have we thought about the right means and ways to recycle Li-Ion batteries? And are we vigilant of the ill impact should we fail to find an answer?
The proliferating demand for Li-ion batteries
Among the various types of batteries available in the market such as lithium-ion batteries, solid-state batteries, nickel metal hydride batteries, lead acid batteries, and ultracapacitors, lithium-ion batteries are the most widely used in EVs today, driven by their high energy per unit mass, high power-to-weight ratio, high energy efficiency, high-temperature performance, and low self-discharge.
The cumulative stock of lithium-ion batteries in India is approximately ~22GWh with applications spread across electronics, stationary, and transportation sectors. The growing trend of electrification across the nation is expected to further push the demand for batteries in the coming years.
The Battery Afterlife
Implications, Challenges, and Roadmap Ahead
While it can’t be argued that EVs are an important component of the net-zero emission targets globally, the challenges imposed on the environment once the batteries run their life course are something that demands immediate consideration to stop irreversible damage ecologically and economically.
What is battery afterlife?
The end of life for Li-ion batteries is a subject of debate and can be broadly put under two categories.
- Traction batteries, ones that allow electric vehicles to run, are considered unfit post losing 20% of their rated capacity, primarily because they don’t meet the range requirements
- Stationary storage batteries typically run till they lose 30-40% of rated capacity
Depending on the use profile of the batteries, they typically last for 5-15 years and still contain >60% of capacity after their end of life, containing a significant amount of critical battery materials.
Li-ion Battery Chemistry
The underlying chemistry of Li-ion batteries defines their performance characteristics. While there have been several cell chemistries introduced over the past decade, the most widely acceptable chemistries today are lithium nickel manganese cobalt oxide (NMC), lithium iron phosphate (LFP), and Lithium Titanate Oxide (LTO).
Here’s a detailed overview of the three chemistries:
Lithium Nickel Manganese Cobalt Oxide (NMC)
In the NMC chemistry, the cathode is made up of a combination of nickel, manganese, and cobalt. Though the material ratio varies for different manufacturers, the common combination is 60% Nickle, 20% Manganese, and 20% Cobalt. The NMC batteries despite having high-specific energy have low stability when compared to other chemistries.
Lithium Iron Phosphate (LFP)
In LFP chemistry, iron phosphate is used as the cathode material and the anode is made up of graphite combined with a metallic current collector grid. The LFP batteries have excellent thermal stability and enhanced safety.
Lithium Titanate Oxide (LTO)
In the LTO chemistry, the anode is made up of lithium-titanate nanocrystals, enabling the electrons to enter and exit the anode very quickly, in turn, making the LTO batteries one of the fastest-charging in the industry. With high thermal stability and safety, the LTO batteries have huge potential in EVs, military, and aerospace industries.
Battery Afterlife | Ecological Implication
With no proper recycling infrastructure in place at present, approximately 9 million batteries are expected to hit landfill in India by 2030. The current commercial Li-ion batteries contain transition metal oxides or phosphates, aluminium, copper, graphite, organic electrolytes containing harmful lithium salts, and other chemicals, which if end up in landfill can pose a grave threat to human health and the overall environment. Moreover, it is extremely complex and expensive to clean up the leaked chemicals, causing both the environment as well as the economy to pay a heavy price for the irresponsible battery disposal.
Battery Afterlife | Economical Implication
For a country like India where there is a dearth of battery-grade materials, the dumping of batteries signifies a massive opportunity and economic loss. With significant capital spent on raw material outsourcing, the country undergoes a huge loss against each battery being dumped without extracting the maximum potential out of it.
The batteries even at the end of their life have more than 50% of their capacity, which implies, that for each battery hitting the landfill, there is massive wastage in terms of raw materials. This further creates a hindrance in the nation’s vision of becoming self-reliant for its energy needs and increases India’s dependence on other countries for its EV tech requirements.
Recycling
The importance of battery recycling cannot be emphasized enough, both from an environmental and economical perspective. However, the recycling of waste li-ion batteries is a highly cost as well as energy-intensive process.
The lithium-ion batteries are subjected to a variety of processes before they are put to recycling due to their complex structure. The batteries are classified and pre-treated through a series of processes such as discharge or inactivation, disassembly, and separation before putting in for recycling.
Two major chemical processes are being deployed for the leaching, separation, extraction, and electrochemical precipitation of li-ion batteries currently on a global scale.
Hydrometallurgical Process
Playing an essential role in extracting rare and strategic metals, the hydrometallurgical process is used in extracting metals in ion form from the black mass in successive steps such as leaching, purification, and recovery of targeted metal by selective precipitation.
Pyrometallurgy
A highly energy-intensive process, pyrometallurgy is a heat-based extraction and purification process in which the Li-ion batteries are heated at a temperature range of between 1200°C and 1600°C. The process basically includes three steps – roasting, smelting, and refining.
Though the current battery recycling infrastructure in India is not viable from the economical as well as technological perspective, it is crucial to ramp up our efforts in this direction to create a circular loop for critical battery materials and ensure resource efficiency.
Roadmap Ahead Toward Realizing an Energy-Self-Reliant India
For India to become energy self-reliant, it is critically important to facilitate an advanced infrastructure for end-of-life battery management. While there are developments taking place on this front, it may take more than a decade for the nation to be well-equipped with a proper recycling setup.
The next question to answer is what can be done to slow down the damage, if not completely stop it, during this timeframe.
Repurposing
Repurposing implies putting the battery to more than one application, thus increasing its utility, and extending its operational time where they contribute towards a green environment. For example, an EV battery after reaching 20% in the traction stage can be put into another application such as stationary storage, wherein the battery could perform efficiently with the remaining capacity after first use. Taking this approach would extend the life of the battery from an application perspective and churn out the maximum potential of the battery before it reaches its saturation.
For an organization aiming to achieve Net Zero, this opportunity for repurposing the batteries would add an extra dimension towards reducing their scope 3 emissions. Scope 3 emissions arise from the activities of assets not owned or controlled by the reporting organization, but that the organization affects in its value chain indirectly.
Approximately 75% of the emissions are generated from the upstream and downstream activities of the company’s value chain, making Scope 3 emissions a critical opportunity toward making a positive difference to the company’s carbon emissions. Some of the 15 scope 3 emissions include “transportation and distribution” along the upstream and downstream value chain, business travel, outsourced employee commute infrastructure, and personal commute by employees.
Given current grid emission factors, the carbon footprint generated by an EV is 30% less than an ICE vehicle. However, if the same EV is powered by renewables, the vehicle’s carbon footprint can go down by more than 90%. On an average, assuming an annual runtime of > 40,000 km, the absolute annual emissions of a 2W, 3W, and 4W, can be brought down to 2 tonnes, 5 tonnes, and 7.3 tonnes, respectively, should the electric vehicles be powered through renewable sources.
With technological innovations in the EV battery space, today’s batteries can have a life span of more than 15 years. Considering a typical EV life of 5-6 years, the batteries can be repurposed for secondary EV applications and then toward tertiary stationary storage applications, augmenting the potential of renewable energy sources such as windmills or solar panels while increasing grid flexibility, stability, and operating economics. By utilising erstwhile EV batteries, brands may enable their net-zero transition while being economically viable and reducing their reliance on the traditional grid.
Extending the life span of batteries
Repurposing batteries is only viable if the overall lifespan of the batteries is amplified. This approach would help the nation with a time-bandwidth to build a fully-fledged recycling process. The longer battery life would stretch the saturation period of the batteries enabling their multiple uses, thereby extending the period by which the batteries would be hitting the landfill.
Log9 | Pioneering solutions for the future
Marching with the motto of Pioneering Responsible Energy, Log9 is always at the forefront of the fight against climate change. To realize the word ‘sustainability’ for the electric mobility space, in entirety, we fine-tuned our technology to deliver the perfect balance between conscience and commerce.
Our RapidX range of batteries, with LTO technology at its core, have a lifespan of more than 15 years and is one of the safest and fastest-charging in the Li-ion battery category.
The long life of Log9’s RapidX batteries enables them to be used for a minimum of 2-3 applications. For instance, after finishing its first life applications and hitting 20% of its rated capacity while deployed in a 3W, the batteries can be utilized in stationary storage applications such as a telecom tower which requires lesser DOD and can run efficiently with the remaining capacity. The multiple application scope enables churning out maximum potential against each battery.
Though the Li-ion battery recycling infrastructure is at a nascent stage at present, there are massive efforts, both in the public as well as private sectors, to equip the nation with a fully-fledged, technologically advanced recycling setup. As per a report by JMK Research, recycling of li-ion batteries will create a USD 1 billion opportunity in India by 2030. Needless to say, there would be a whole new dimension added to the energy self-reliance vision of the nation upon the realization of a localized recycling infrastructure.
Shikha Sinha
Manager - Content Strategy and Development
Rajat Singh
Sustainability & Stationary Energy Storage - Founders Office